Rotoform S8
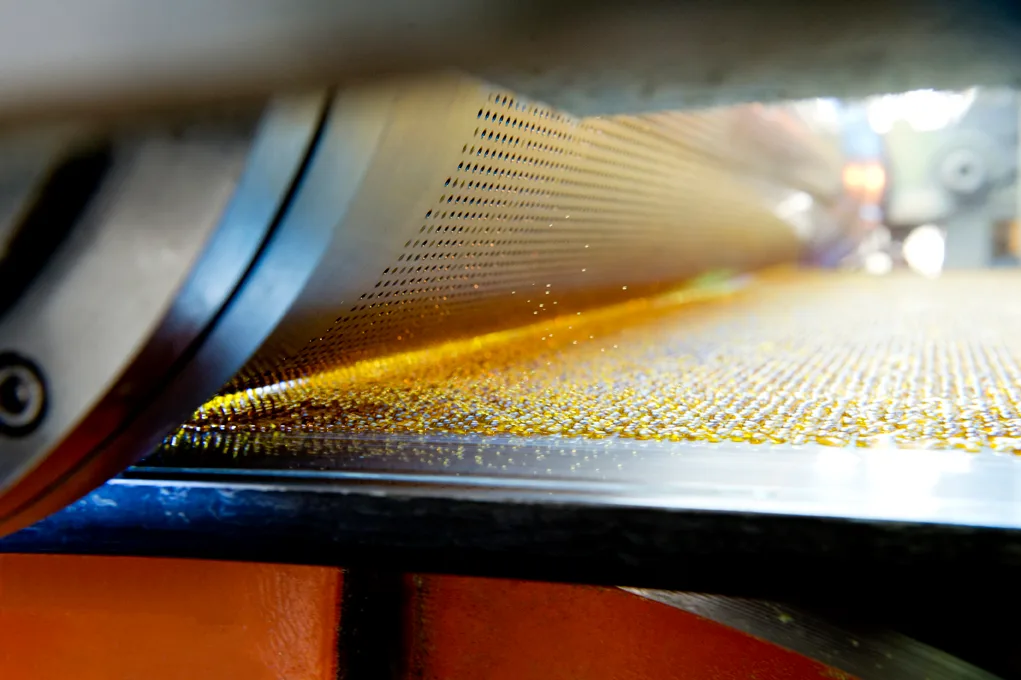
Rotoform S8
The Rotoform S8 is optimized for sulphur solidification. It is designed to meet small- to mid-size capacity sulphur processing requirements and is the world’s most widely used process for the production of premium quality solid sulphur pastilles.
If your business needs to convert sulphur into solid pastilles of uniform shape, stability and quality, the Rotoform S8 can help.
The Rotoform S8 is optimized for sulphur solidification. It is designed to meet small- to mid-size capacity sulphur processing requirements and is the world’s most widely used process for the production of premium quality solid sulphur pastilles.
If your business needs to convert sulphur into solid pastilles of uniform shape, stability and quality, the Rotoform S8 can help.
Premium sulphur solidification for small/medium- capacity requirements
Sulphur is usually produced in liquid form at 125–130 °C, making it difficult – and expensive – to transport, handle and store. The Rotoform S8 converts this low-viscosity melt into Sulphur Development Institute of Canada (SUDIC) premium quality pastilles, drawing on our experience with over 700 sulphur installations. It is designed for efficient processing at small- to mid-capacity installations:
On-stream factor of c. 97%
Unrivalled product uniformity
Direct-from-the melt pastillation
The sulphur pastillation process is environmentally friendly in that production is virtually dust free, emissions are very low due to the speed of solidification, and there is no risk of cross-contamination with the cooling water.
Where higher capacity is needed, our Rotoform HS is a high-speed model with a throughput rate of up to 15 tons/hour.
Maximum sulphur processing flexibility
Multiple S8 units can be installed alongside one another. Individual lines can be shut down – and restarted – in minutes, enabling overall capacity to be adjusted to meet changing throughput rates.
Sulphur is usually produced in liquid form at 125–130 °C, making it difficult – and expensive – to transport, handle and store. The Rotoform S8 converts this low-viscosity melt into Sulphur Development Institute of Canada (SUDIC) premium quality pastilles, drawing on our experience with over 700 sulphur installations. It is designed for efficient processing at small- to mid-capacity installations:
On-stream factor of c. 97%
Unrivalled product uniformity
Direct-from-the melt pastillation
The sulphur pastillation process is environmentally friendly in that production is virtually dust free, emissions are very low due to the speed of solidification, and there is no risk of cross-contamination with the cooling water.
Where higher capacity is needed, our Rotoform HS is a high-speed model with a throughput rate of up to 15 tons/hour.
Maximum sulphur processing flexibility
Multiple S8 units can be installed alongside one another. Individual lines can be shut down – and restarted – in minutes, enabling overall capacity to be adjusted to meet changing throughput rates.
Rotoform S8 credentials
Proven
700+
Rotoform sulphur installations
Versatile
10 mPas
Maximum viscosity handled
Capacity
5.5 tons/hour
Maximum handling capacity
How it works
Rotoform S8
Like all Rotoform lines, the Rotoform S8 combines a drop depositor with a steel belt-based cooler. Drops of molten sulphur are deposited onto the moving belt by means of a perforated rotating shell that turns concentrically around a heated stator.
The heat of the drops is transferred via the steel belt cooler to water sprayed underneath, resulting in rapid solidification. The solidified droplets are discharged from the steel belt as uniform hemispherical sulphur pastilles.
Like all Rotoform lines, the Rotoform S8 combines a drop depositor with a steel belt-based cooler. Drops of molten sulphur are deposited onto the moving belt by means of a perforated rotating shell that turns concentrically around a heated stator.
The heat of the drops is transferred via the steel belt cooler to water sprayed underneath, resulting in rapid solidification. The solidified droplets are discharged from the steel belt as uniform hemispherical sulphur pastilles.
Benefits
Why choose pastillation with IPCO Rotoform?
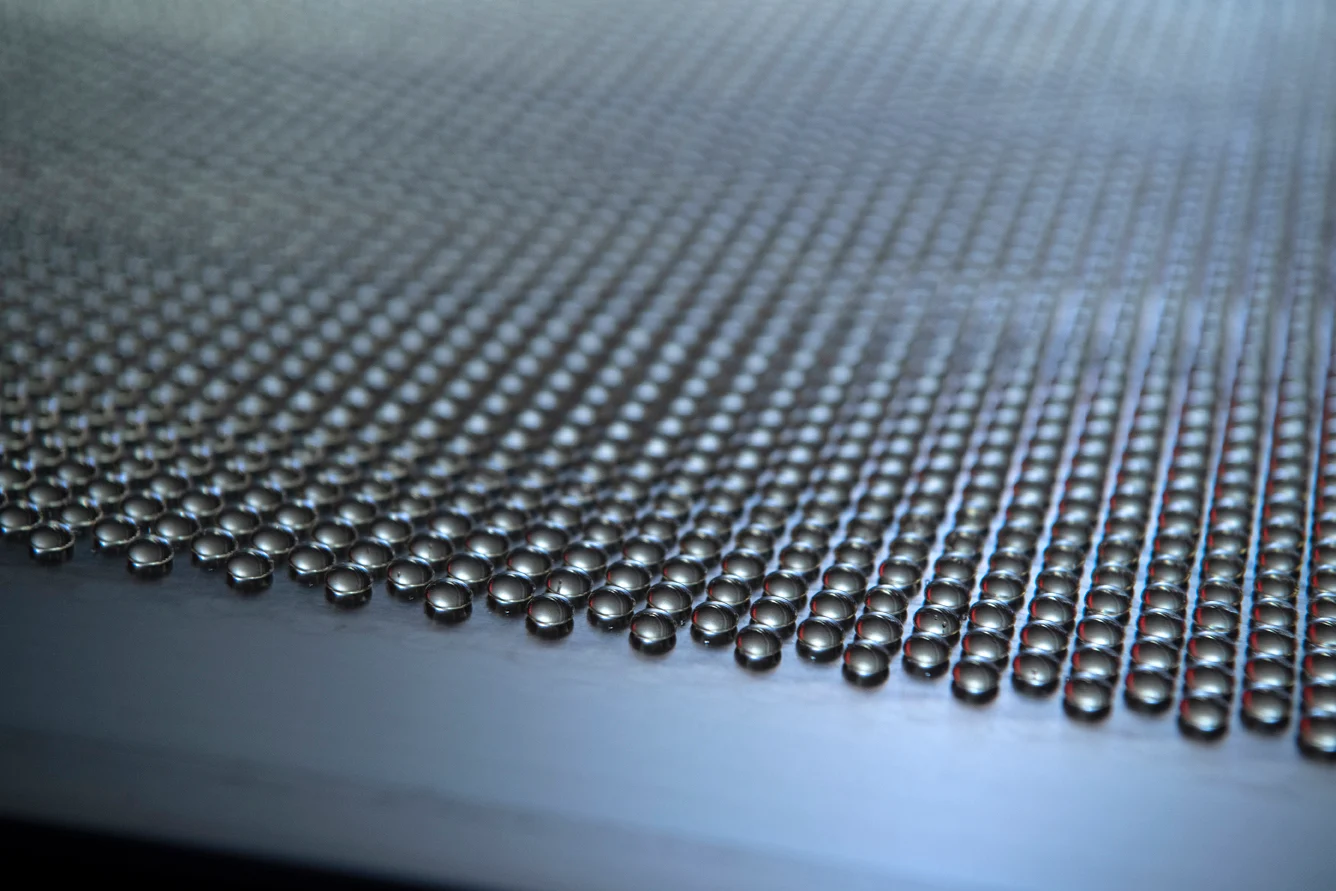
Benefits
Rotoform systems
Direct from-the-melt solidification
Consistent pastille shape and size
High bulk density for storage and packing
Free flowing for easy handling, storage and reprocessing
Environmentally friendly production – dust-free, no risk of cross contamination of cooling water
Very low vapor/ gas emissions
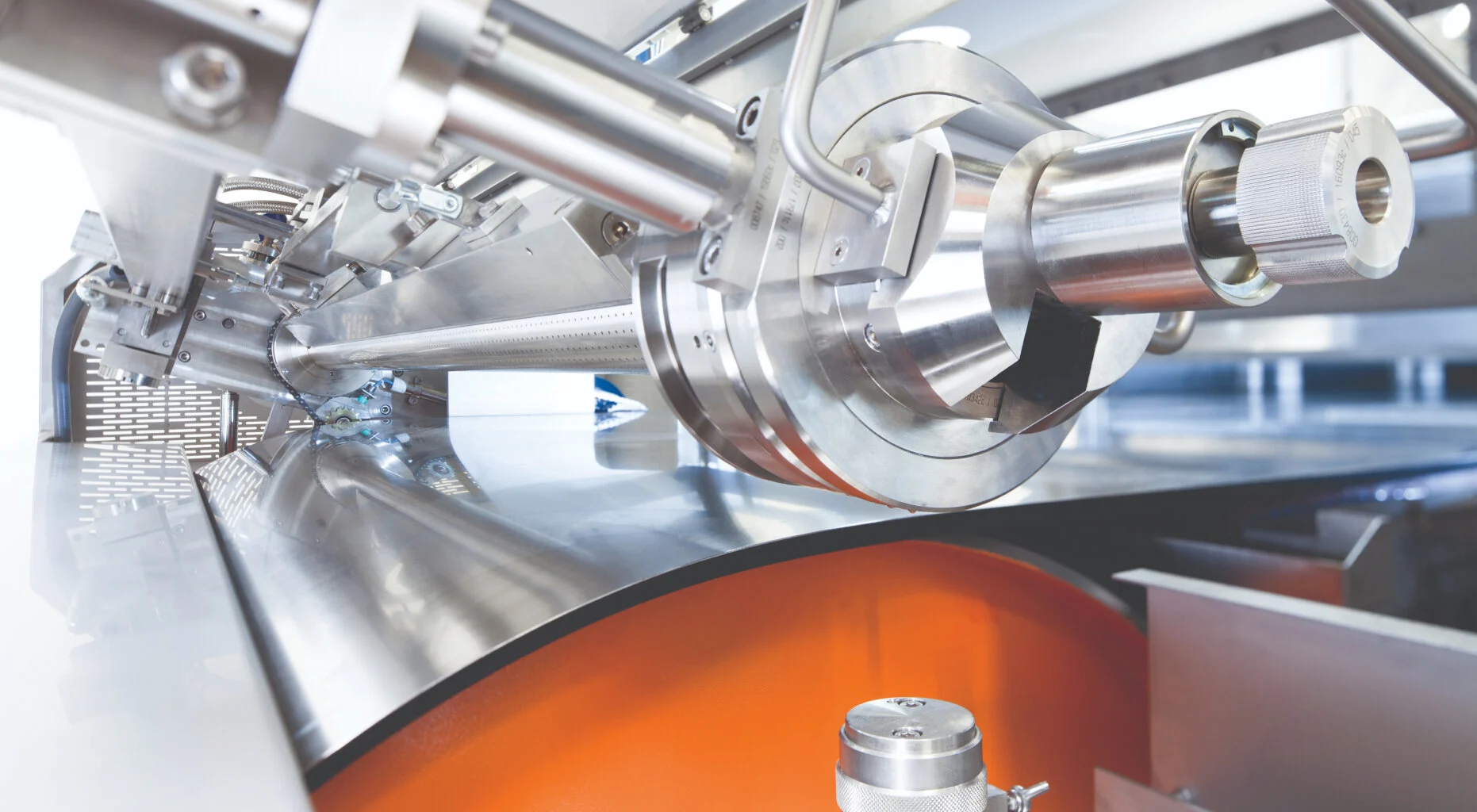
Benefits
Designed for sulphur pastillation at medim/high capacity
The Rotoform S8 delivers on all the key requirements of the sulphur processing industry, including:
SUDIC premium quality pastilles
Low friability, minimizing product degradation and dust
High angle of repose, good flow characteristics
High purity and consistent quality
Low residual H2S (< 10 ppm)
Low moisture content (the IPCO Rotoform process does not increase the moisture content)
Unrivalled uniformity
Technical
Specifications
Temperature (max): 125–145 °C
Viscosity (max): 10 mPas
Pastille size: 3–5 mm
Capacity (max): 5.5 t/h
Typical products: sulphur
Temperature (max): 125–145 °C
Viscosity (max): 10 mPas
Pastille size: 3–5 mm
Capacity (max): 5.5 t/h
Typical products: sulphur
Use this solution for
Processes supported
Pastillation
Solidification systems for chemical melts with a high feed temperature
Portfolio showcase
Our Rotoform portfolio
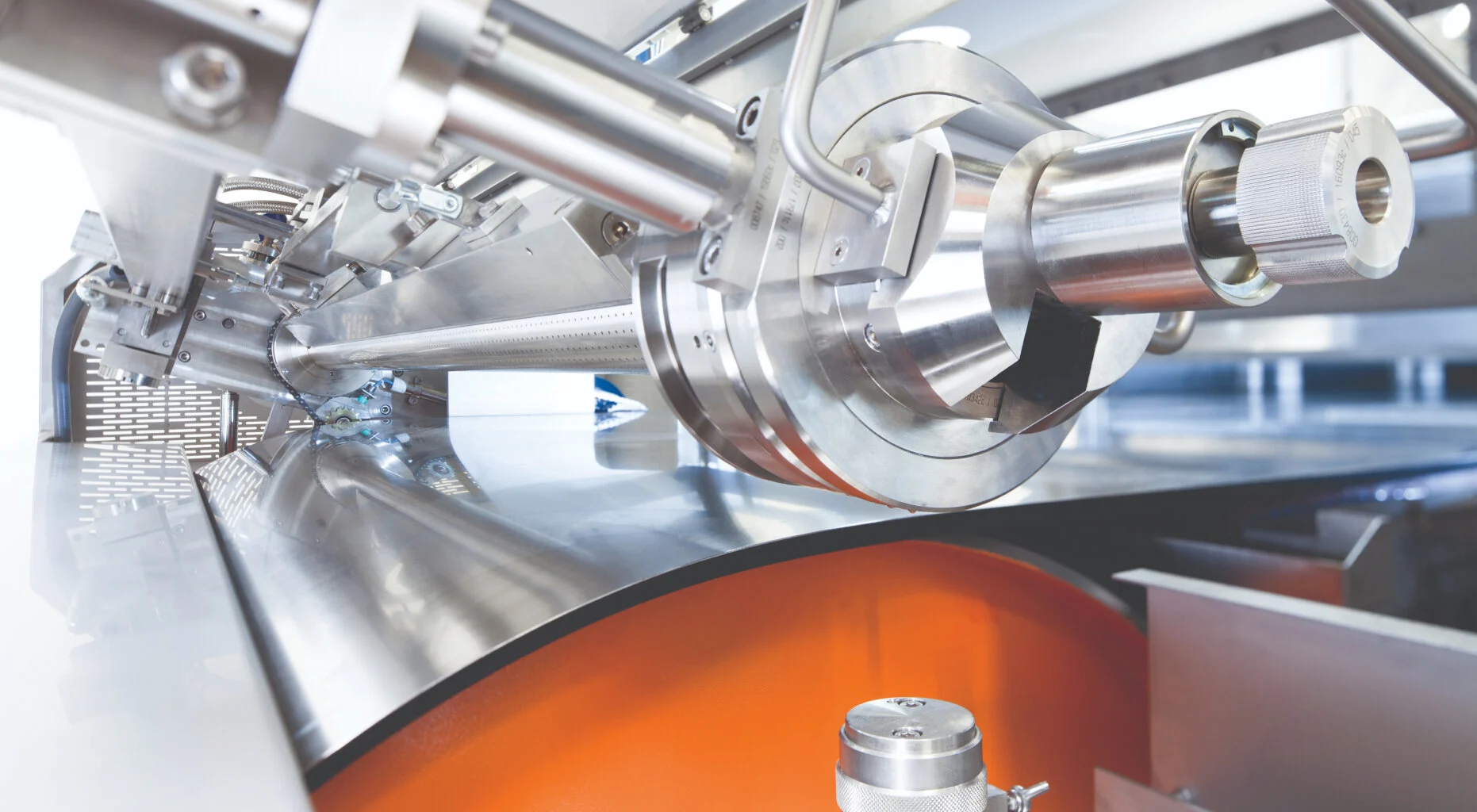
Rotoform 4G
Standard solution for low- and high-viscosity melts
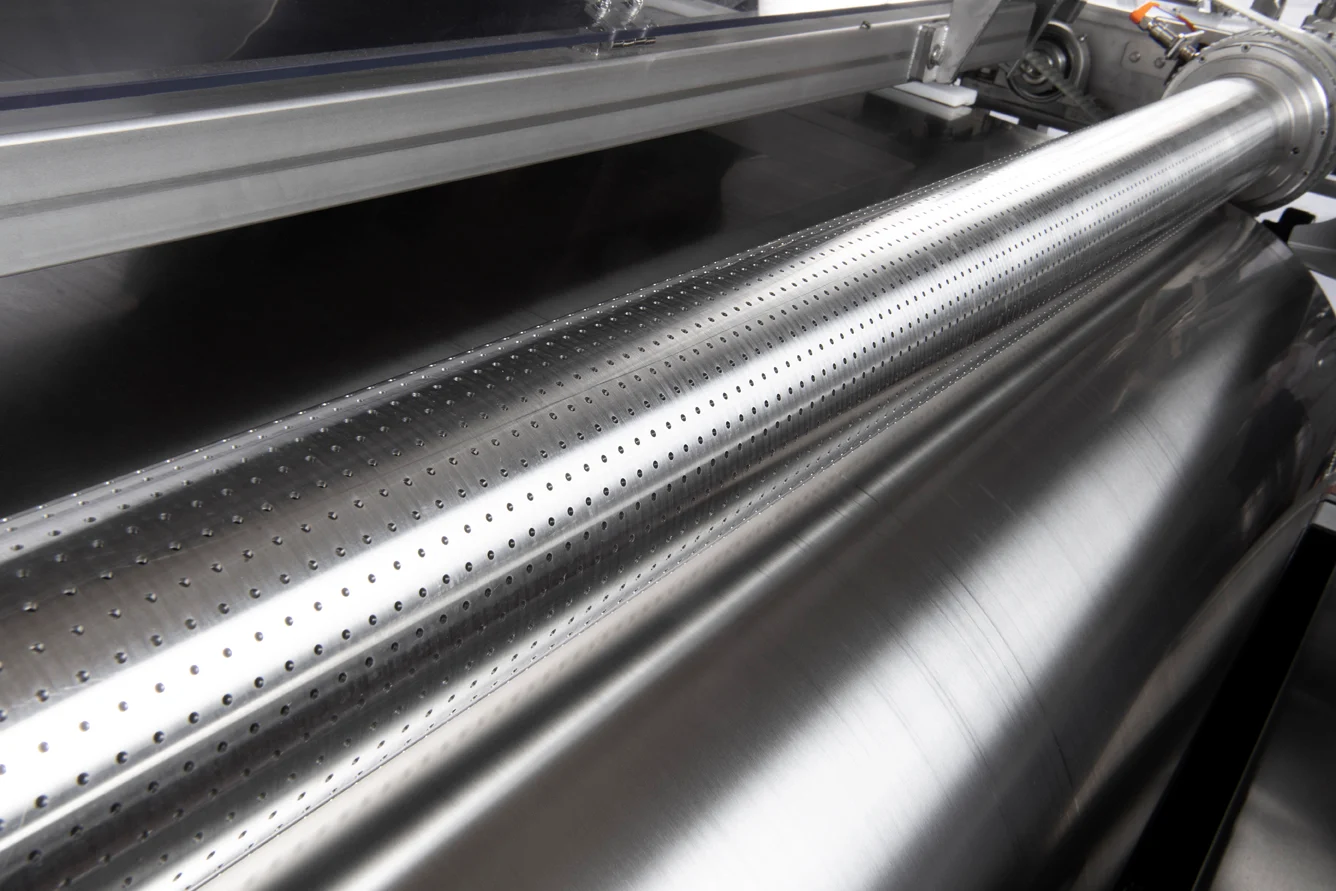
Rotoform 4G CR
For corrosive products
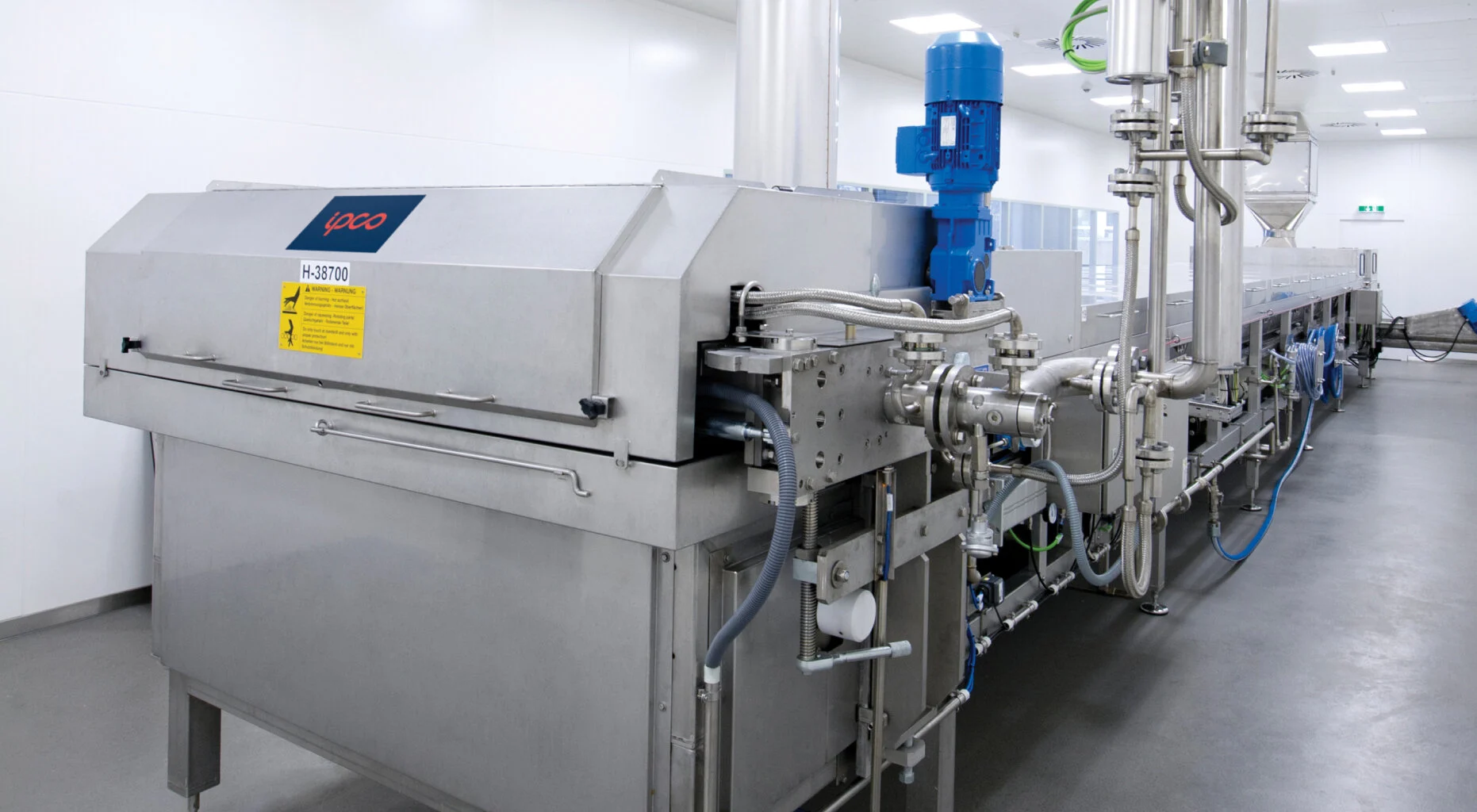
Rotoform 4G FD
For the food industry, e.g. hygiene, easy dismantling/cleaning
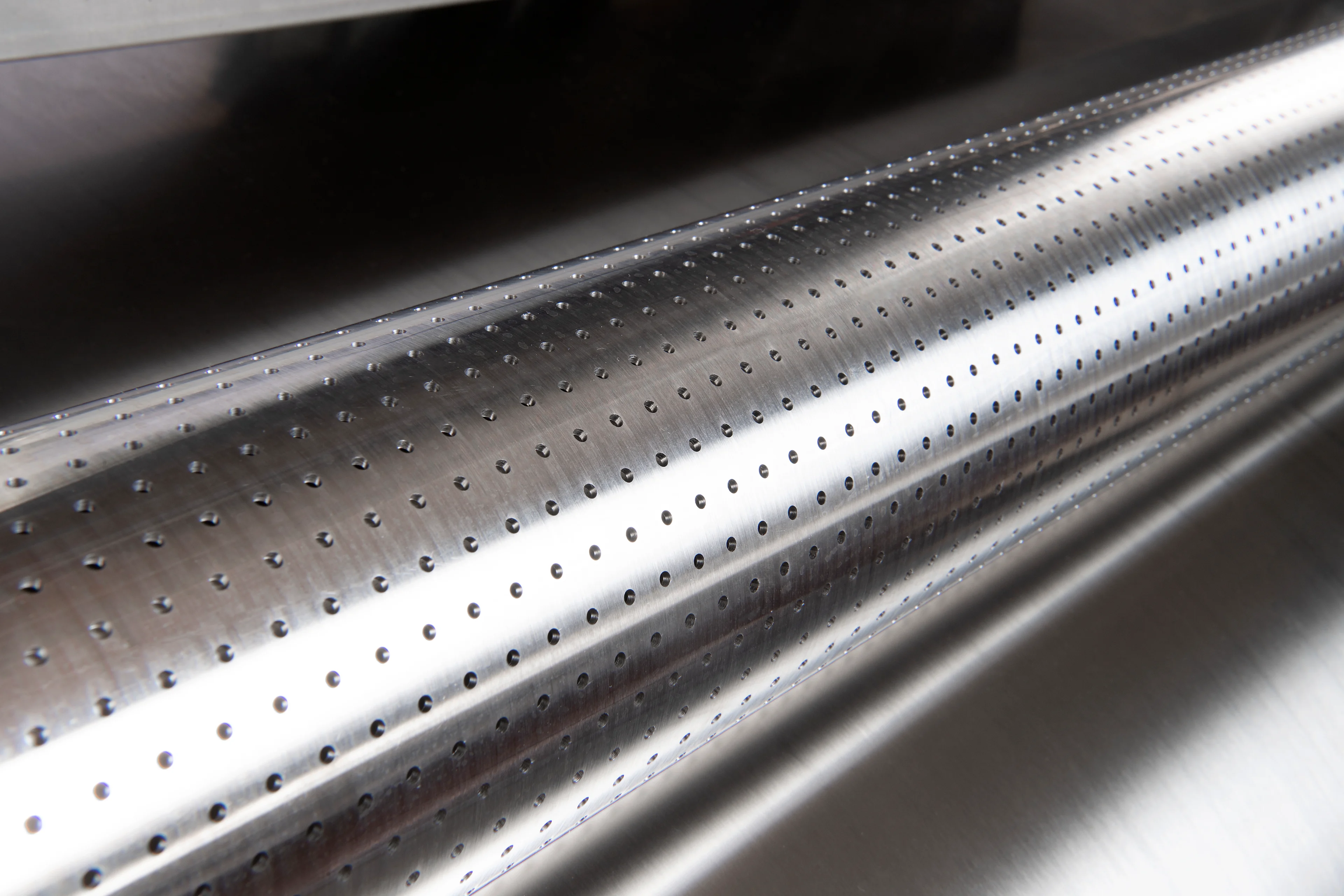
Rotoform 4G HT
For melts that feed at high temperature (up to 300°C)
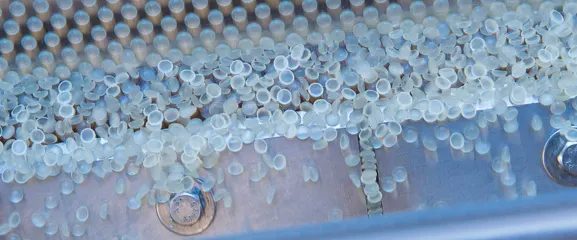
Rotoform 4G MC
For micropastilles down to 0.8mm diameter
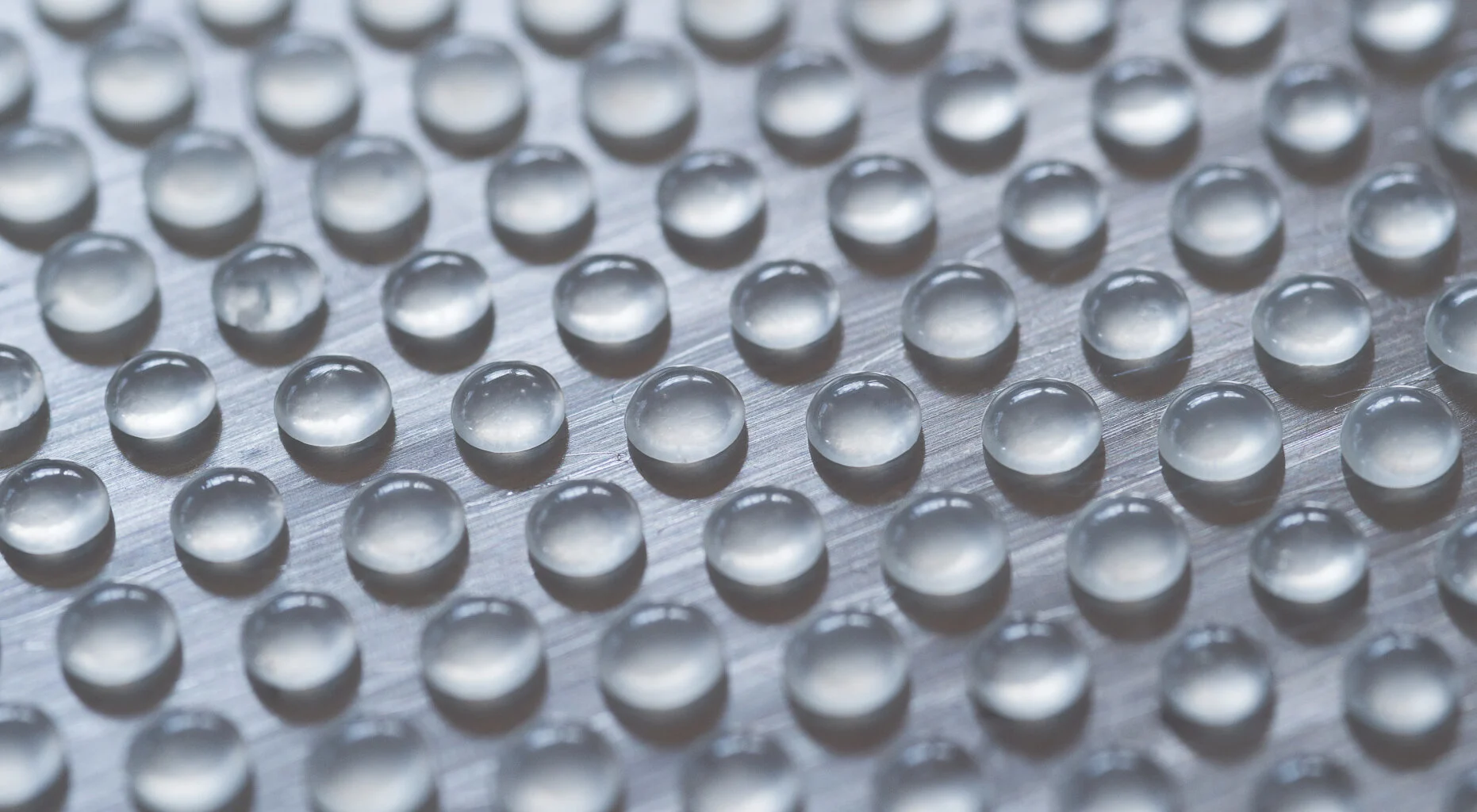
Rotoform 4G SC
For subcooling melts in supercooling plants
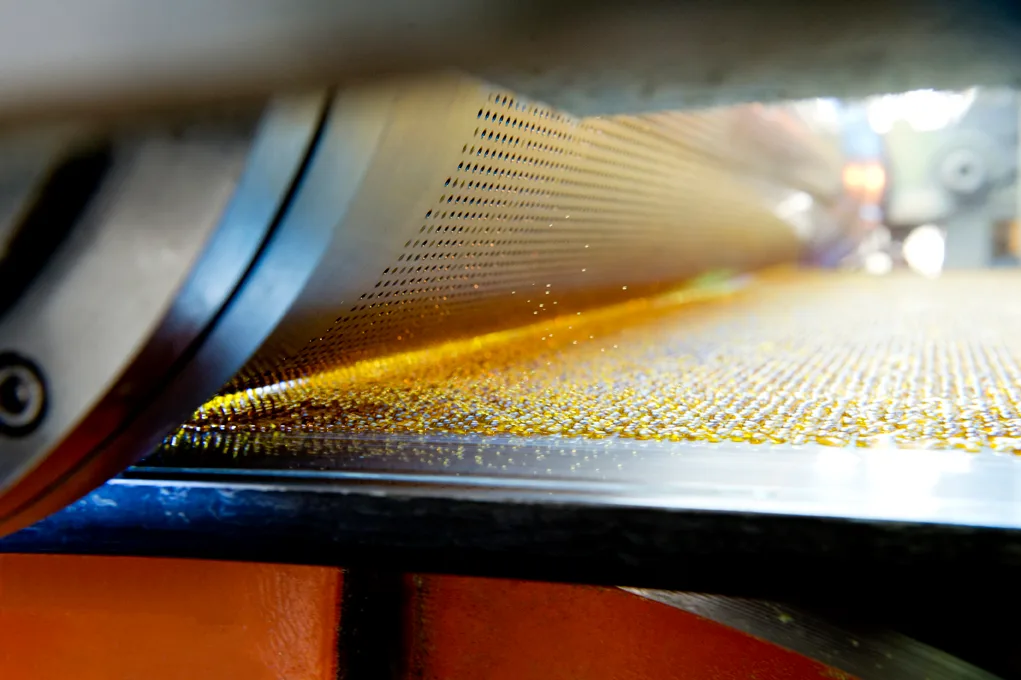
Rotoform S8
For the particular requirements of sulphur pastillation
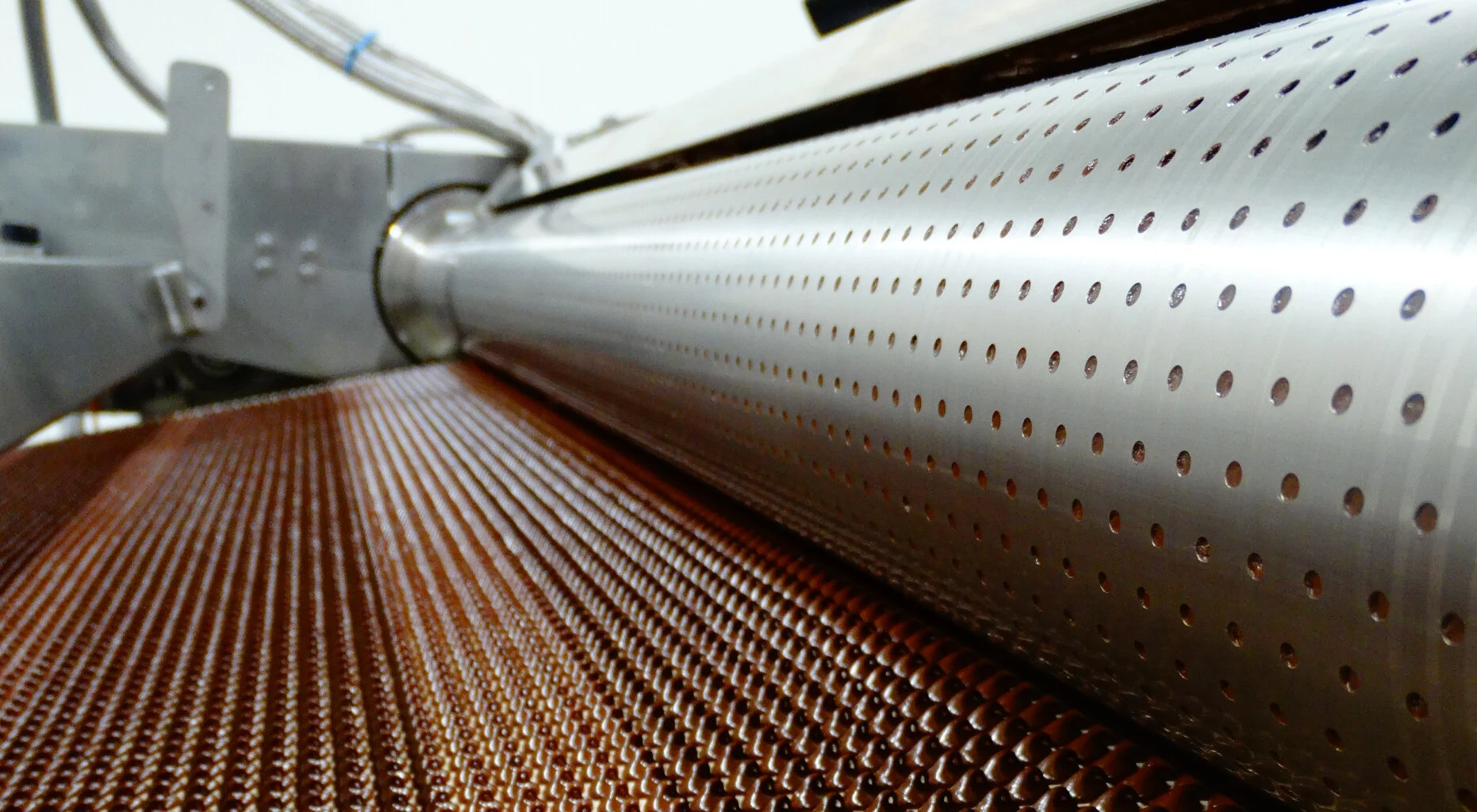
Rotoform HP
For increased homogeneity
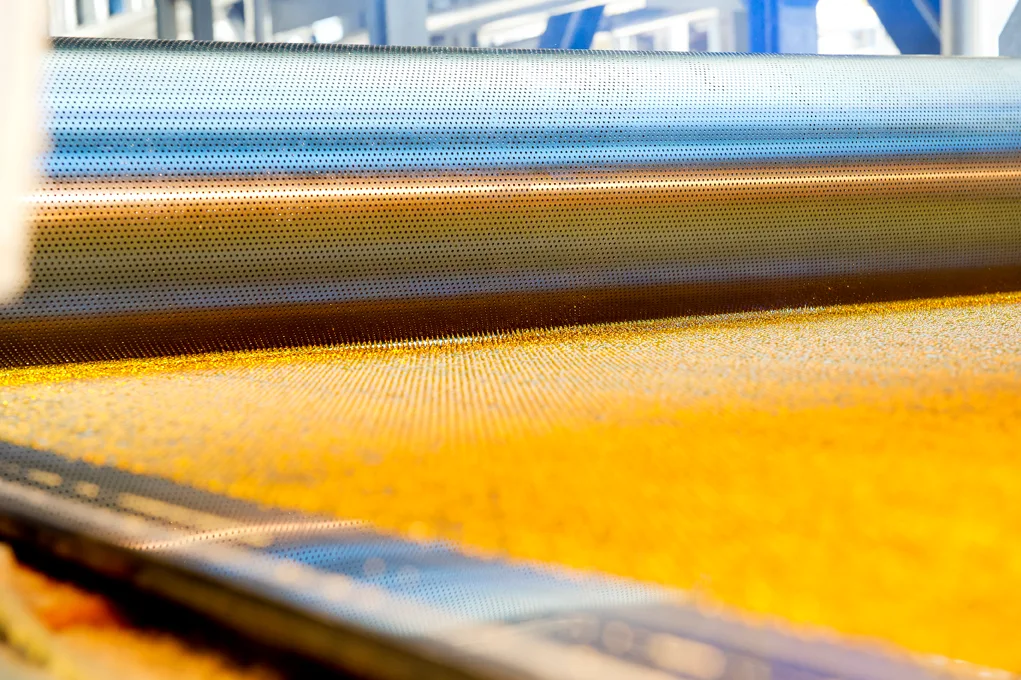
Rotoform HS
For high-speed, high-capacity pastillation of lower-viscosity products
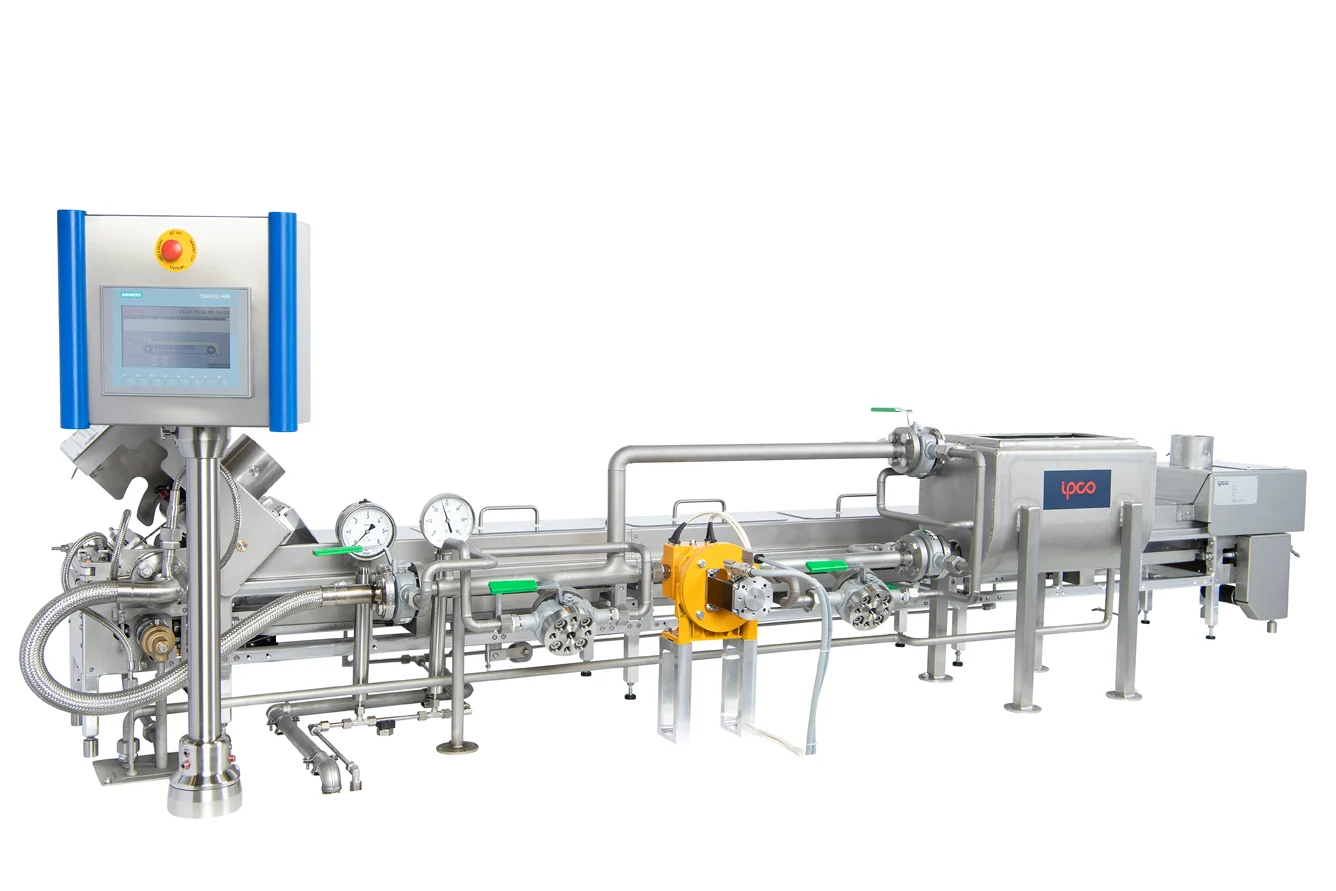
Rotoform MI
For laboratory use, R&D, and small capacity production (<20 kg/h)
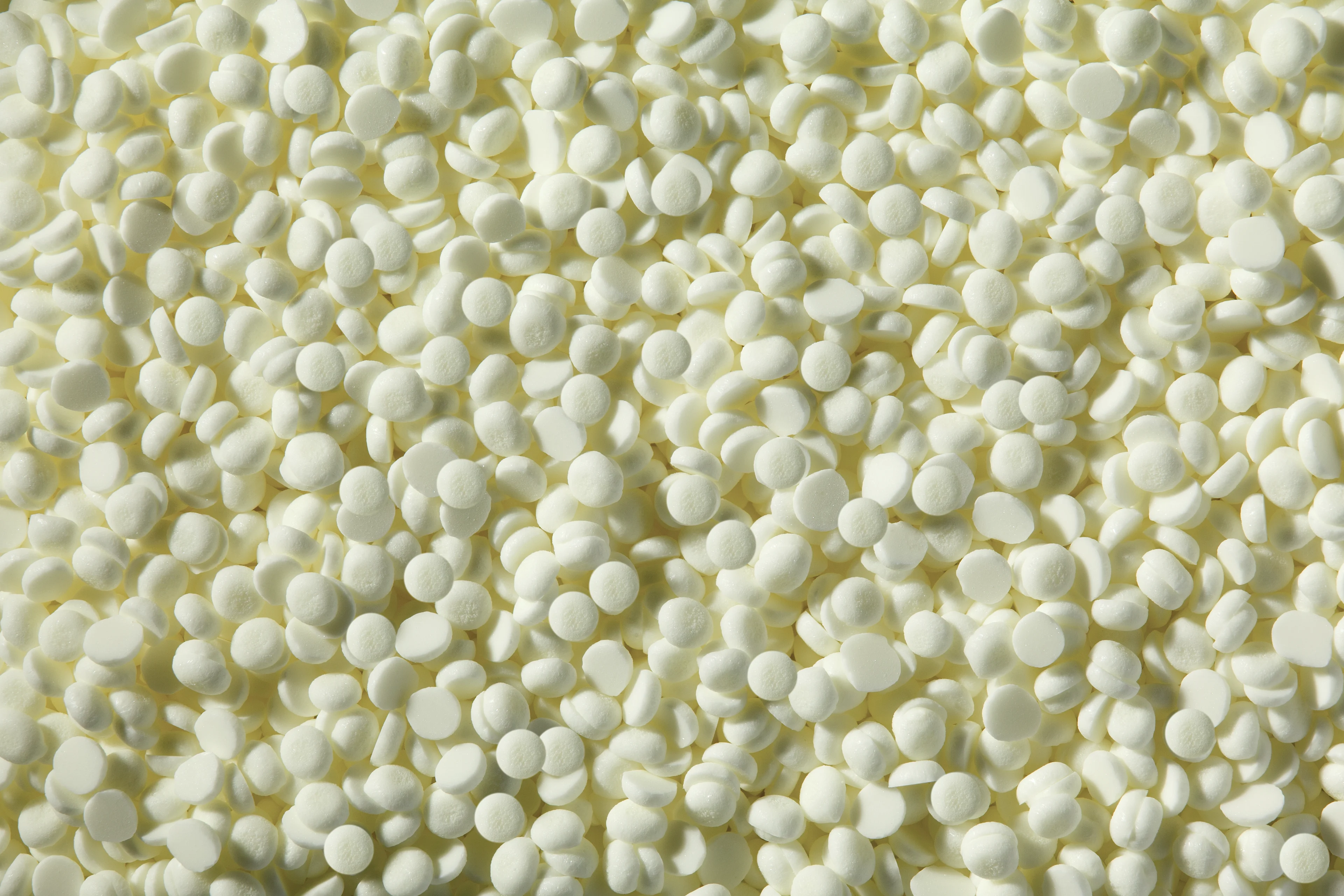
Rotoform XG
For high-capacity pastillation of low-viscosity melts containing solid particles (suspensions)
Get in touch
We believe strongly in collaboration and love to share our knowledge and experience. Fill out the form, and one of our experts will contact you shortly.